Last Updated on August 1, 2023 by Kevin Chen
Introduction
Membrane Bioreactor (MBR) technology has become a highly efficient solution for wastewater treatment, with the advantages of excellent effluent quality and compact design. However, as with any technology, it has its challenges. One of the most critical problems faced in the operation of MBR systems is fiber breakage in the MBR membranes.
Understanding fiber breakage is crucial for anyone operating, maintaining, or managing an MBR system. Fiber breakage can lead to reduced system performance, increased maintenance costs, and, in some cases, may require expensive membrane replacement. By thoroughly understanding what causes fiber breakage, how to prevent it, and what to do if it occurs, we can ensure the longevity and efficiency of our MBR systems.
This article will explore the causes and consequences of fiber breakage and effective prevention and remediation strategies. We will also introduce SPERTA’s reinforced PVDF hollow fiber, which effectively solves the fiber breakage problem and provides a robust and reliable solution for MBR systems.
Understanding MBR Membrane Fiber Breakage
What is Fiber Breakage?
In a membrane bioreactor (MBR) system, a fiber break is the physical damage or rupture of the hollow fiber membrane used for filtration. These fibers are typically made of materials such as polyvinylidene difluoride (PVDF) and are designed to be both robust and permeable, allowing water to pass through while filtering out contaminants.
However, these fibers may become brittle or subjected to stresses beyond their structural capacity over time and under certain conditions. This can lead to fiber breakage, where the fibers physically split or fracture. This damage may be localized, affecting only a small portion of the fiber, or more extensive, affecting a large fiber length.
Fiber breakage is a severe problem in MBR systems because it compromises the integrity of the filtration process. Broken fibers allow contaminants to pass through unfiltered, which can degrade the quality of the treated water and potentially cause harm to downstream processes or the environment.
How To Detect Fiber Breakage?
Detecting fiber breaks in MBR membranes can be complex due to the system’s complexity. However, several methods can be used to identify broken fibers:
Visual Inspection: Periodic visual inspections of the membrane module can help identify broken fibers. This includes checking the fibers for any visible signs of damage, such as fraying, splitting, or complete breakage.
Performance Monitoring: A sudden drop in system performance or an unexpected increase in transmembrane pressure (TMP) can indicate fiber breakage. These changes occur because the broken fibers allow larger particles to pass through, reducing the overall filtration efficiency of the system.
Permeate Turbidity: Increased permeate (filtered water) turbidity can also indicate fiber breakage. Broken fibers may allow larger particles and contaminants to pass through, causing the permeate to become more turbid.
Automated Monitoring Systems: Some advanced MBR systems are equipped with automated monitoring systems that can detect changes in performance parameters and indicate potential fiber breakage. These systems provide real-time alerts so that immediate action can be taken.
What causes Fiber Breakage?
Fiber breakage in membrane bioreactor (MBR) systems can be caused by a number of factors, including:
Physical Stress: Excessive physical stress on fibers can lead to breakage. This can be due to improper handling during installation, maintenance, or mechanical forces within the system, such as high flow rates or turbulence.
Chemical Damage: Certain chemicals can degrade the fiber material, making it more susceptible to fracture. This can occur if the MBR system is exposed to harsh cleaning chemicals or the treated wastewater contains corrosive substances.
Thermal stress: Extreme temperatures can also cause fibers to break. Higher temperatures make fibers more brittle, while lower temperatures reduce their flexibility. Both of these conditions increase the risk of breakage.
Aging and Wear: Over time, the fibers in an MBR system will naturally degrade due to continued water flow and contaminant filtration. This wear and tear can eventually lead to fiber breakage.
Misoperation: Operating the MBR system outside the recommended parameters can also lead to fiber breakage. This includes running the system at too high a pressure or not performing regular maintenance and cleaning.
Understanding these causes of fiber breakage can help develop strategies to prevent this problem and extend the life of your MBR system.
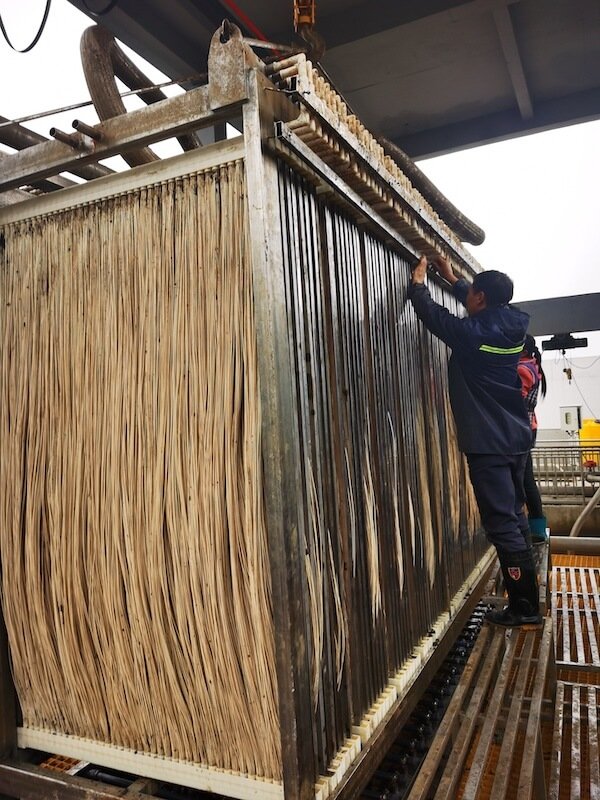
Consequences of Fiber Breakage
What Are the Impacts on Filtration Performance?
Reduced Filtration Area: When fibers break, the total effective area available for filtration is reduced. This reduction can result in a lower permeate flow rate, meaning that the system treats less water in the same period.
Increased Transmembrane Pressure (TMP): Fiber breakage can increase the TMP, which is the difference in pressure at the membrane surface. A higher TMP means that the system needs to work harder to push water through the membrane, resulting in increased energy consumption.
Decreased water quality: Broken fibers allow solids to pass through the membrane and contaminate the permeate (filtered water). This contamination can reduce the quality of treated water, potentially making it unsuitable for its intended use.
Increased likelihood of clogging: Broken fibers can lead to an uneven flux distribution across the membrane surface, raising the possibility of fouling. Fouling and accumulating unwanted material on the membrane surface can reduce the permeate flux and increase the TMP.
What Are the Impacts on the Economic?
The economic implications of fiber breakage in MBR membranes can be substantial and include the following:
Increased Maintenance Costs: Broken fibers often need to be repaired or replaced, which can be a significant expense, especially if breaks are frequent. In addition, labor costs associated with these maintenance tasks can add up quickly.
Operational Downtime: The MBR system may need to be shut down when maintenance is required to address fiber breakage. This downtime can disrupt operations, especially in industrial settings where continuous wastewater treatment is critical.
Higher Energy Costs: As mentioned earlier, fiber breakage can increase transmembrane pressure (TMP), which means the system needs to work harder to filter the water. This increased effort leads to increased energy consumption, which increases energy costs.
Potential Loss of Revenue: For commercial operations that sell treated water or use treated water in their processes, a decrease in water quality due to fiber breakage could result in a loss of revenue. If the water quality does not meet the required standards, it may not be sold or used, thus impacting the bottom line.
Replacement Costs: In severe cases, large-area fiber breaks may require replacement of the entire membrane module. These replacements can be a significant expense, especially for larger MBR systems.
Prevention Strategies for Fiber Breakage
Proper Operation and Maintenance Procedures
Ensuring MBR membranes’ longevity and optimal performance requires adherence to proper operation and maintenance procedures. These procedures are designed to prevent fiber breakage and extend the life of the membrane.
Regular Cleaning: Regular cleaning of the MBR membrane is essential to prevent the buildup of solids and biofilm on the membrane surface. This buildup can increase the stress on the fibers and lead to breakage. Cleaning procedures can include backwashing, chemical cleaning, and air flushing.
Monitor Operating Conditions: It is essential to monitor the operating conditions of the MBR system continuously. This includes monitoring transmembrane pressure (TMP), flux rate, and permeate quality. Any sudden changes in these parameters can indicate problems with the membrane fibers.
Prevent overloading: Overloading an MBR system can stress the membrane fibers excessively and cause breakage. It is important to ensure the system is not overloaded and the flow rate is within the recommended range.
Regular Maintenance: Regular maintenance of your MBR system is critical to prevent fiber breakage. This includes replacing worn parts, checking fiber integrity, and ensuring the system operates efficiently.
By following these procedures, operators can significantly reduce the risk of fiber breakage and ensure the long-term performance of the MBR system.
Importance of Regular Inspections
Regular inspections play a vital role in preventing fiber breakage in MBR systems. They allow for early detection of potential issues, enabling timely intervention and minimizing the risk of severe damage.
Early detection of breakage: Regular inspections help detect early signs of fiber breakage. This includes visible signs of wear, changes in permeate quality, or fluctuations in system operating parameters.
Membrane condition assessment: Inspections provide an opportunity to assess the overall condition of the membrane. This includes checking the fibers’ integrity, the membrane surface’s cleanliness, and the module housing’s condition.
Verify operating conditions: During the inspection, the operator can verify that the system’s operating conditions are within the recommended range. This includes checking transmembrane pressures, flux rates, and influent quality.
Maintenance Planning: Periodic inspections can inform a maintenance program by identifying components that may need to be replaced or repaired. This helps prevent unexpected failures and ensures the system operates at peak efficiency.
In short, regular inspections are a critical preventative measure against fiber breakage. They ensure that the MBR system is kept in optimal condition, thereby extending the life of the membranes and maintaining high filtration performance.
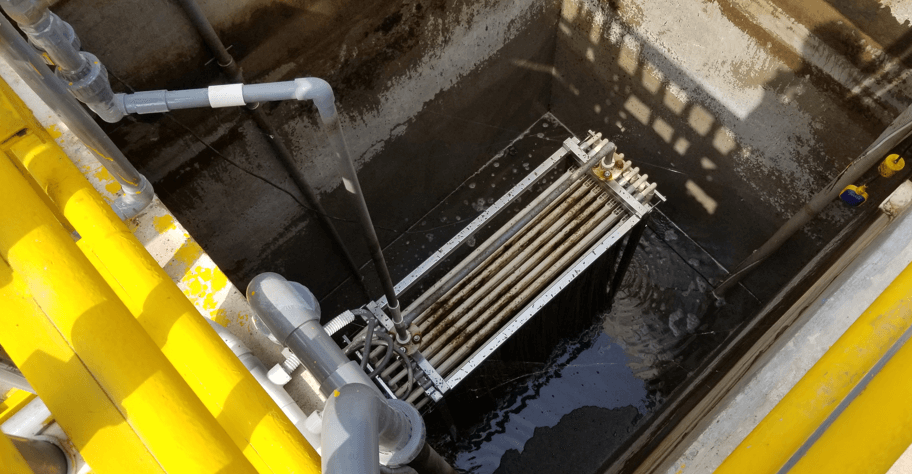
Role of High-Quality Membranes
The quality of the membranes used in MBR systems is an essential factor in preventing fiber breakage. High-quality membranes are designed to withstand the harsh conditions of wastewater treatment and offer several advantages:
Durability: High-quality membranes are typically made of robust materials that can withstand the harsh conditions of wastewater treatment. This includes resistance to chemicals, temperature changes, and mechanical stress, all of which can cause fiber breakage.
Performance: High-quality membranes provide consistent performance over their lifetime. They maintain their permeability and rejection properties, ensuring that treated water quality remains high. This reduces the likelihood of operational problems that can lead to fiber breakage.
Longer life: High-quality membranes typically have a longer operational life. They are less likely to break prematurely, reducing the need for frequent replacements and associated downtime.
Support: Manufacturers of high-quality membranes often provide comprehensive support, including detailed operating and maintenance instructions. This support helps operators optimize processes and prevent conditions that could lead to fiber breakage.
Investing in high-quality membranes can significantly reduce the risk of fiber breakage. While their upfront cost may be high, their performance, longevity, and support benefits can reduce the total cost of ownership over the system’s life.
Remediation Measures for Fiber Breakage
Repair Methods for Broken Fibers at End Port
For leaks detected at either end of the membrane fiber, we can take the below steps:
- Remove the membrane from the cassette and cut the damaged fibers 20 mm from the ABS header. Regarding the correct cutting position, see the figure below.
- Using a syringe filled with silicone sealant, insert the tip of the needle 10mm into the center of the fiber. for the injection position, see the figure below.
- Inject silicone under light pressure. Begin removing the needle slowly to ensure the fiber is completely filled. While still pressurizing the syringe, use the tip of the needle to place silicone over the fiber of the cut head.
- Once the repair is complete, put the MBR membrane module back to the MBR tank.

If the leak is in the middle of the fiber, follow the steps below.
- Remove the membrane element from the cassette. Using a hypodermic syringe filled with silicone sealant, insert the tip of the needle into the membrane fiber. Be careful not to puncture the membrane, just to its hollow center. For insertion instructions, see the figure below. The needle is properly positioned 5 to 10 mm from the leak area at a 5 to 10 degree angle.
- Inject silicone under light pressure. Fill 5 to 10 mm beyond the leak area. Continued pressure while removing the needle from the fiber should ensure that the hole is sealed.
- Once the repair is complete, put the MBR membrane module back to the MBR tank.
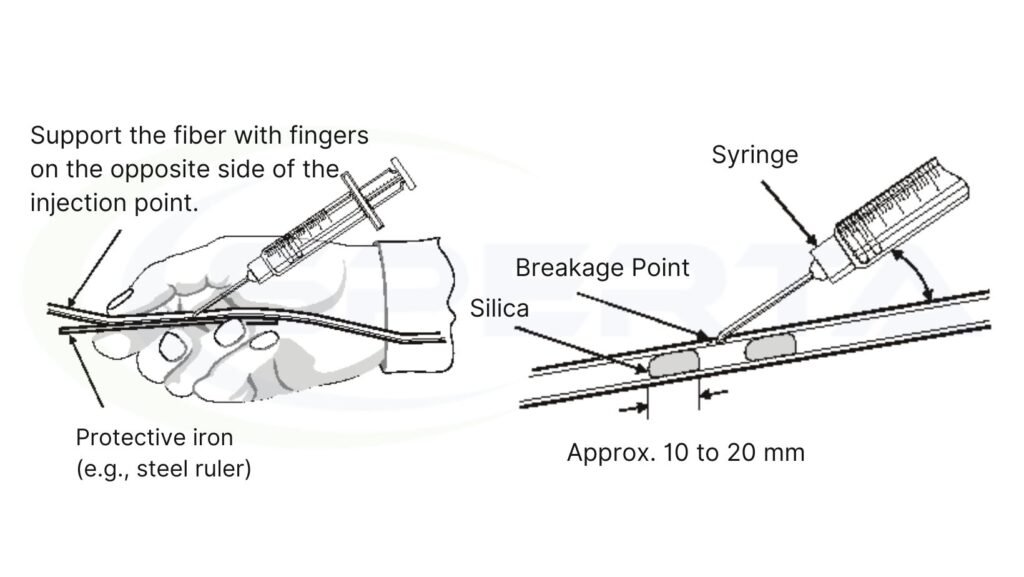
Guidelines for MBR Membrane Replacement
Replacing the MBR membrane is an important task that requires careful planning and execution. Here are some guidelines to follow when replacing your membrane:
Assess the situation: Before deciding to replace the membrane, it is essential to assess the situation thoroughly. This includes determining the extent of the damage, understanding the cause of the breakage, and considering whether repair is a more appropriate option.
Choose the suitable replacement: If replacement is necessary, ensure the new membrane is high quality and suitable for your particular system. It should have the same specifications as the original membrane to ensure compatibility and performance.
Follow the manufacturer’s instructions: Always follow the manufacturer’s instructions when replacing membranes. This will help ensure proper and safe replacement. It is also important to use the proper tools and equipment.
Test After Replacement: After replacement, it is critical to test the system to ensure the new membrane is working properly. This includes checking for leaks and evaluating the performance of the system.
Regular Maintenance: After replacement, continue to perform routine maintenance and inspections. This helps prevent future breakage and extends the life of the membrane.
Remember, membrane replacement should be performed by a trained professional or under professional supervision to ensure safety and effectiveness.
Minimizing Operational Impact
When fiber breakage occurs, it can disrupt the normal operation of an MBR system. However, there are ways to minimize the operational impact and maintain the system’s efficiency.
First, it is critical to have an emergency response plan in place. The plan should outline the steps to be taken during a fiber break, including immediate actions to prevent further damage and a long-term strategy for system recovery.
Second, regular inspections and maintenance can help identify potential problems before they escalate. Recognizing and addressing minor damage early can prevent major system failures and costly downtime.
Finally, investing in high-quality membranes, such as SPERTA’s reinforced PVDF hollow fibers, can greatly reduce the risk of fiber breakage. These fibers can withstand harsh conditions and prolonged use, ensuring reliable and consistent performance.
By implementing these strategies, you can effectively minimize the operational impact of fiber breakage and ensure the longevity and efficiency of your MBR system.
SPERTA’s Solution: Reinforced PVDF Hollow Fiber
Unique Features of SPERTA’s Hollow Fiber
SPERTA’s Reinforced PVDF Hollow Fiber is a breakthrough in membrane technology. It employs a unique reinforcement technique that enhances the structural integrity of the fiber. It is strong, durable, and resistant to physical stress, chemical damage, and thermal changes. The fiber’s unique design also ensures optimal filtration performance, making it ideal for MBR systems.
How SPERTA’s Fiber Solve the Fiber Breakage Problems
SPERTA’s reinforced PVDF hollow fibers solve the problem of fiber breakage. The reinforcing technology used in its construction increases the fiber’s resistance to physical stress, reducing the risk of breakage during installation, maintenance, and operation. In addition, the chemical resistance of the fibers prevents them from degrading due to harsh cleaning chemicals or corrosive substances in treated wastewater. This extends the fibers’ life and reduces the MBR systems’ maintenance costs.
Performance Benefits of SPERTA’s Fiber
SPERTA’s reinforced PVDF hollow fibers offer a variety of performance advantages. Its robust construction ensures high reliability and longevity, reducing the need for frequent replacement. The superior filtration performance of this fiber produces cleaner, higher-quality effluent. In addition, the fiber’s resistance to chemical and thermal changes ensures consistent performance, even under challenging operating conditions. All of these factors contribute to MBR systems’ operational efficiency and cost-effectiveness.
Conclusion
Proactively managing fiber breaks is critical to maintaining the efficiency and longevity of MBR systems. By choosing a solution like SPERTA’s reinforced PVDF hollow fibers, operators can significantly reduce the risk of fiber breakage and associated maintenance costs. This not only ensures consistent system performance but also results in cleaner, higher-quality effluent.
Have questions or need more information? Please feel free to contact us. Our team of experts is ready to help you with any questions about our products and how they can benefit your MBR system. Contact SPERTA today and let us help you optimize your wastewater treatment process.