Last Updated on July 24, 2022 by Kevin Chen
The sewage entering the MBR tank is oxygenated by the blower and biodegraded. And the clean water separated by the membrane enters the storage tank or discharges directly.
The equipment can be controlled automatically or manually. If it is found that the MBR reactor is not running normally, it should be dealt with or reported to the relevant maintenance department in time. The operator must be familiar with the treatment process and facilities’ operational requirements and technical indicators.
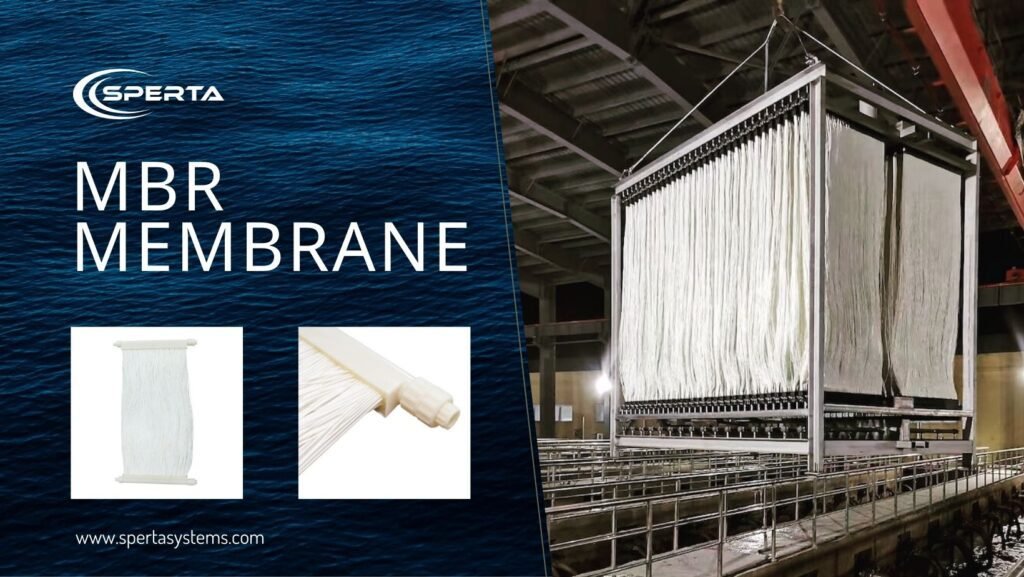
MBR System Commissioning
Commission the equipment after installation. After meeting the requirements, you can move to the next step. There are the following processes:
(1). After the equipment is installed, check the operation of the equipment with clean water, and make a record first:
Step 1: Turn on the blower to supply air into the MBR tank and observe the operation condition of the blower & aeration system.
Step 2: Fill the MBR tank with clean water to the required water level of the floating ball. When the water in the tank reaches above the floating ball water level, the suction pump will automatically start. The suction pump will automatically stop when the water level drops below the floating ball water level.
Step 3: Debug the equipment with load for 1 hour until the equipment usually runs.
Note: The water pump is only tested for 5 minutes in step 3 above. Observe whether the pump is usually working, whether the vacuum gauge is standard, and the condition of the water outlet pipeline. Do not run the water pump for a long time.
(2). Microbial domestication and cultivation until the water quality reaches the standard:
Step 1: Enter the sewage to a high water level and start the blower at the same time. It is recommended to inoculate activated sludge to speed up the cultivation process and add appropriate nutrients for suffocation.
Step 2: When the sludge concentration in the reaction tank exceeds 3000~6000mg/l, and the activated sludge properties are good, turn on the suction pump and make it in the state of automatic control. The water output should not be too large and should be controlled at the rated value of 1/3 to 1/2. At the same time, control the amount of water in and out.
Step 3: when the sludge concentration in the reaction tank exceeds 6000~12000mg/l and the effluent quality reaches the standard, the effluent quantity can be adjusted to reach the rated value.
In the above process, when the sewage temperature is 15-20 degrees, this stage will take around 30 days. When the initial sludge concentration of the reaction tank is 3000mg/l by inoculating the activated sludge of the sewage treatment plant, the microbial domestication and cultivation time can be shortened by about 1/3 to 1/2, and the cultivation in winter may take 30-45 days.
MBR Membrane Operation
Preparations should be made before starting the system. MBR adopts two control modes, automatic and manual. The initial operation control gauge’s vacuum degree is less than 0.01MPA.
In automatic mode, the suction pump runs automatically in the following manner according to the set program.
(1). The suction pump is linked with the blower. If the blower stops, the suction pump stops automatically.
(2). When the water reaches the low water level of the MBR tank, the suction pump starts, and when the water level in the clean water tank is high, it stops. The blower and the suction pump are linked, run periodically for 13 minutes, and stop for 2 minutes.
A: When the negative pressure of the barometer reaches 0.04MPA, the alarm light will alarm.
B: When the water is below the low water level, the suction pump stops, but the blower runs periodically for 60 minutes and off for 30 minutes. In any case, the suction pump only runs when the blower is running.
C: When the vacuum degree of the vacuum gauge is greater than 0.05MPA caused by the blockage of the membrane, it will alarm and stop and can only be reset manually. Under normal circumstances, the sludge concentration in the MBR tank for domestic sewage treatment is 6000-12000 mg/l, and the average concentration of dissolved oxygen is not less than 2 mg/l.
Note: The average working temperature of the MBR system should be in the range of 5-40 degrees. When the ambient temperature is lower than 0 degrees, the water in the system must be released when it stops running to avoid freezing. Store in an environment above freezing point. Otherwise, it will easily cause permanent damage to the MBR membrane.
Turning on the suction pump to discharge water under the following conditions will seriously damage the MBR membrane and affect the life of the module:
The water level in the tank does not submerge the MBR membrane.
The activated sludge is abnormal.
The aeration stopped.
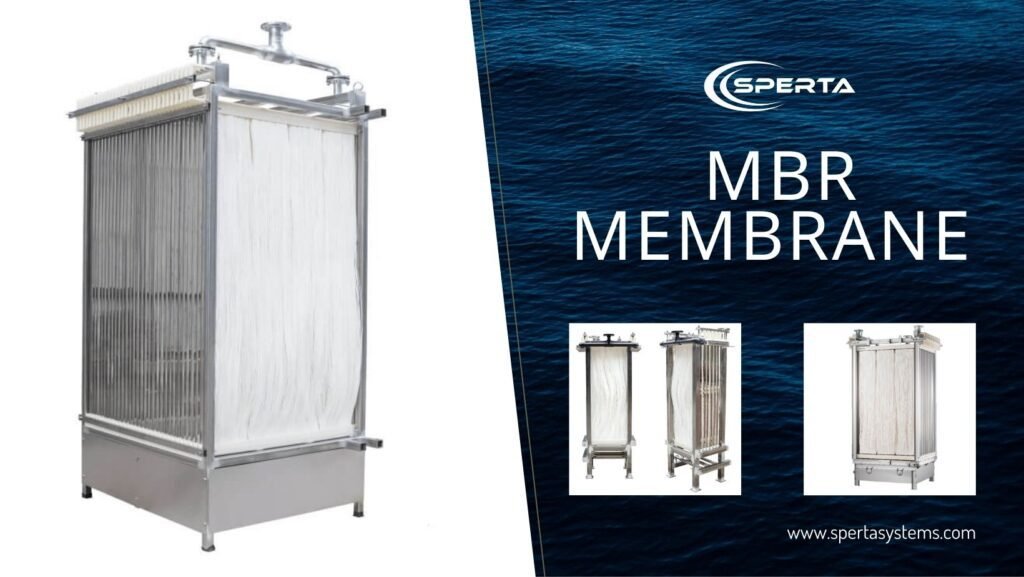
MBR Membrane cleaning
Membrane cleaning must be performed by professionals.
The membrane module is operated at a predetermined flow rate. The initial pressure difference between the membranes is about 10KPa. After the membrane module has been filtered for a while, pollutants accumulate on the surface of the membrane, causing the pressure difference between the membranes to rise. When the pressure difference between the membranes is 20KPa higher than the initial stage, it is necessary to conduct chemical cleaning. Chemical cleaning must be performed when the differential pressure is 30KPa higher than the initial steady-state differential pressure.
When the operating system conditions are kept stable, online cleaning every 3-6 months can restore the water flux of the MBR membrane. At this time, the membrane energy is about 80-95% of the original initial state.
If the membrane module is used for a long time without chemical cleaning, the deposits on the membrane surface will be solid, and the effect of online chemical cleaning will not be good. When the membrane flux cannot be restored by online chemical cleaning, offline chemical cleaning should be concerned.
In order to restore the performance of the MBR membrane well, it is recommended to take online chemical cleaning in the early stage when the transmembrane pressure difference has a clear upward trend. When the pressure difference between the membranes is 20KPA higher than the initial stage, please get in touch with the after-sales service or technical department of SPERTA in time.
Troubleshooting
(1). Blower
If the linkage between the blower and the water pump fails, the blower is seriously heated or cannot be turned on. We should turn the power off in time and notify the maintenance department.
Suppose the blower stops running for more than 1 day, especially in summer, which can lead to the death of a large number of microorganisms. If the system stops running for 1-3 days and then restarts, the activated sludge activity should be restored after the blower has been running for 1 day. Then the system should be in an automatic control state, and the water pump will automatically run. If the system stops running for a long time (more than 3 days) and then restarts, the microorganisms must be re-cultured.
(2). Air volume
Suppose it is observed that the agitation of the sewage in the MBR reactor is significantly weakened. You should first check whether the air pipeline is normal, such as air leakage, blocked airflow in the channel, and clogged air intake by the blower filter system.
(3). Water Volume
Suppose the MBR water output is significantly reduced. You should first check whether the vacuum level of the vacuum gauge is normal. When the transmembrane pressure difference is 20KPa higher than the initial stage, and other reasons are ruled out to determine that the membrane surface is blocked, we should consider chemical cleaning.
If the MBR reactor does not produce water, first check whether the water level of the reactor is below the float ball. Secondly, check whether the float ball and the suction pump are invalid. Please notify the relevant maintenance department to replace them if they are invalid.
(4). Water Quality
Suppose the water quality of MBR production water deteriorates. In that case, you should first check whether the MBR membrane and pipeline system are normal and whether the color, state, odor, and concentration of activated sludge are standard. If the pretreatment device is not working properly, it should be promptly excluded. If the pretreatment device is not working properly, the symptoms should be excluded in time. If the concentration of activated sludge is too low or the state is abnormal, we should turn the suction pump off and turn on only the blower to cultivate bacteria. When the sludge concentration in the reactor is 6000-8000mg/L, and the activated sludge activity recovers, turn on the suction pump to discharge the water and put the system in an automatic control state.
(5). Vacuum Degree
Regularly observe the vacuum degree of the vacuum meter. When the vacuum degree of the vacuum meter is greater than 0.04Mpa, you should immediately notify the relevant maintenance department.
(6). Foaming
When the detergent content in the sewage is high, the sludge can produce more foam during the aeration process. If another foam type appears: thick, fatty, creamy in appearance, it’s created when certain types of detergents biodegrade. These detergents contain soluble grease, which cannot be removed in the pretreatment and enter the biological treatment system to form foam, concentrate, and float. This is unavoidable in aeration systems, and it is often associated with excessively long residence times of sewage in the reactor (eg, insufficient load, low flow at night).
When the effluent quality is seriously affected, we can take the following measures:
Add defoamer (use only if defoamer will not damage the membrane).
Water spray to remove.
Increasing the reactor sludge concentration is the simplest and most effective remedy.
If foaming occurs repeatedly, we should remove part of the detergent with raw water to solve the foaming problem. When the detergent content exceeds 40 mg/L, it is harmful to the treatment of organisms.
(7). Sludge color and smell
Good quality activated sludge is dark brown. The black sludge in the reactor usually means the beginning of spoilage. The black sludge often emits the smell of hydrogen sulfide, which is caused by the relatively insufficient aeration. We can take the following measures: suspend the water output or increase the aeration amount.

The Main Conditions For Long-term Stable Operation
(1). To maintain good hydraulic circulation conditions in the bioreactor and possess an excellent hydraulic scouring effect on the membrane surface, the aeration rate should be appropriately increased.
(2). Do a good job in the start-up operation of the reactor, which can increase the concentration of the inoculated sludge, and then start the operation of the membrane separation after the operation of the bioreactor is stable.
(3). Pay attention to the daily maintenance of the membrane. We can adopt simple methods such as air aeration and online chemical cleaning to slow down the growth rate of membrane filtration resistance and prolong the membrane running time.
(4). Maintain stable operating conditions. Frequent changes in operating conditions can promote membrane plugging processes and accelerate membrane fouling.
(5). When using the MBR system, we should pay special attention to the pretreatment of sewage. Before the sewage enters the MBR, a grille below 2mm should be installed. For kitchen drainage with more grease, we should also install high-efficiency oil separation facilities. It is forbidden to directly enter the MBR system with the integrated domestic sewage that has not been treated by the septic tank.
Special Precautions
(1). The MBR system is technologically advanced sewage treatment equipment, but it also has stricter requirements on influent water quality. When the sewage contains many heavy metals, non-biodegradable organics, pesticides, oils, acid and alkali, and other pollutants, it must be pre-treated before entering the MBR system for treatment. SPERTA can provide relevant technical advice.
(2). For the sewage discharge points with intermittent, concentrated, and significant water quality changes, it is necessary to build a regulating tank to adjust the water volume and water quality before entering the MBR system for treatment.
(3). The MBR system requires a continuous operation. Once the aeration is stopped for more than 12 hours, it will lead to the death of many biological organisms, thus affecting the quality of the effluent.
(4). The membrane module needs to be cleaned periodically to maintain the long-term stable operation of the MBR system. If it is not cleaned for more than 3-6 months, it may cause permanent blockage of the membrane module and cannot restore its function.
(5). If the user intends to stop the operation for more than one week, the sewage in the equipment should be emptied, and water should be injected to immerse the mold module. The membrane module must be wholly immersed in clean water and stored in a freezing point environment. Antifreeze should be considered in winter. Otherwise, it will easily cause damage to equipment and components.
(6). The user should establish a system for regular inspection and maintenance of equipment. The content of standard inspection includes:
- Bar screen: Clean the bar screen regularly to prevent the blockage from affecting the water intake.
- Outlet vacuum pressure gauge: Regularly check and record the condition of the vacuum pressure gauge. The vacuum pressure range for regular and stable operation is 0.01-0.04MPa.
- Water quality and quantity of effluent: regularly measure the quality and quantity of incoming and outgoing water and make records.
- Status of activated sludge: regularly check the color of activated sludge and conditionally measure the concentration of activated sludge.
- The operation of other parts of the equipment.

Conclusion
This guide provides an in-depth look at how to operate and manage a MBR membrane. By understanding the process and best practices for MBR membrane operation management, you can ensure that your system is running effectively and producing the best results.
If you have any questions, please leave a comment. We would love to hear from you. And please like and follow us to stay up-to-date on our latest posts.